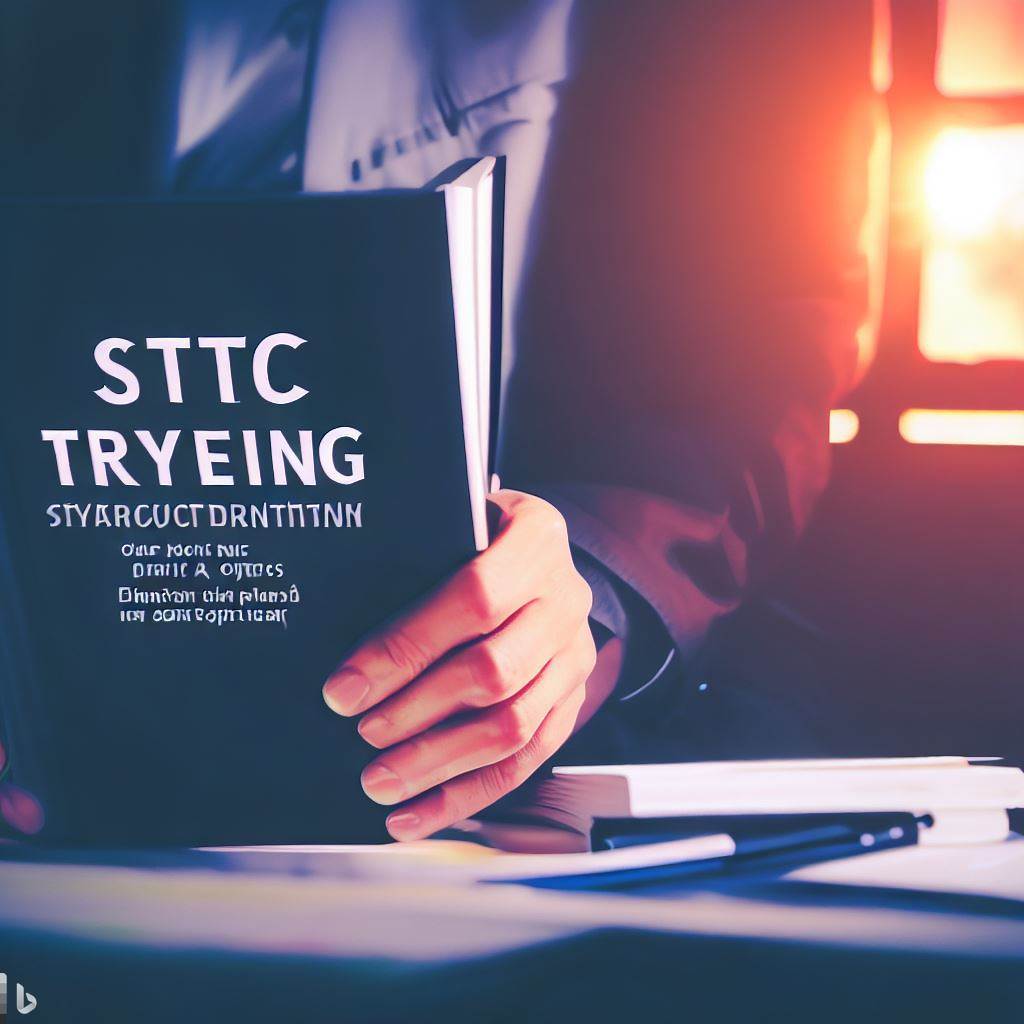
In-House vs. Contract Manufacturing for Lateral Flow Tests: A Strategic Decision-Making Guide
Introduction
In the world of rapid diagnostic tests, lateral flow tests (or lateral flow assays) have become a popular tool, offering quick, easy-to-use, and cost-effective solutions for a wide range of applications, from medical diagnostics to environmental monitoring. The recent global health crisis has further underscored the importance of these tests, tossing them into the spotlight and sparking a surge in research and development efforts. The lateral flow test market has seen significant growth in recent years. This article aims to guide you through the strategic decisions involved in developing and manufacturing lateral flow tests, whether you're considering building an in-house unit or hiring a custom developer or contract manufacturer.
1. The Rising Tide of Lateral Flow Test Research and Development
The past five years have witnessed a significant increase in the number of publications related to lateral flow tests. This surge in research activity reflects the growing recognition of the potential of these tests in various fields. While specific numbers are not readily available (screening just on CrossRef its more than 90% increase; see fig.1), the trend is clear: the lateral flow test field is expanding at an unprecedented rate.
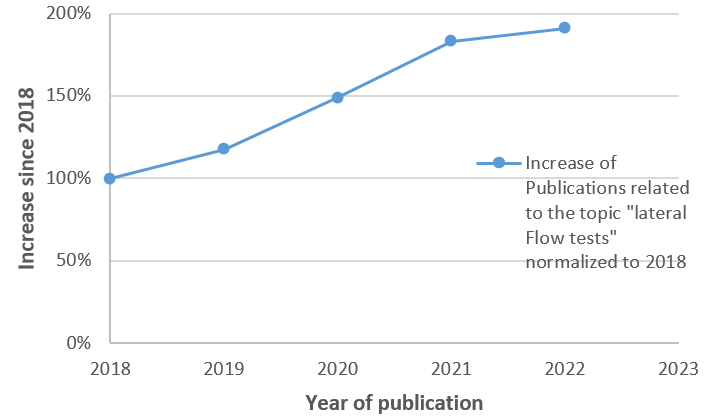
This surge in interest is not surprising. Lateral flow tests offer a unique combination of advantages that make them particularly suited to today's fast-paced, results-driven world. They are quick, often providing results in minutes. They are easy to use, typically requiring no specialized training or equipment. They are versatile, capable of detecting a wide range of targets. And they are cost-effective, making them accessible to a broad audience. The rising tide of research and development activity is driving innovation in the field, leading to the development of new tests, the improvement of existing ones, and the exploration of new applications. It's an exciting time to be involved in lateral flow tests, whether as a researcher, a developer, a manufacturer, a user – or consultant.
Rapid growth also brings challenges. The field is becoming increasingly complex, with a multitude of options and considerations. Whether you're a seasoned veteran or a newcomer, making good decisions in this dynamic landscape can be tricky. That's where this article comes in. In the following sections, we'll explore the different considerations involved in developing and manufacturing lateral flow tests, providing a roadmap to guide your decision-making process.
2: Building an In-House Development and Manufacturing Unit
Building an in-house development for diagnostic test development and in-house manufacturing unit for lateral flow tests is a strategic decision that involves at least the following:
1. Setting up a development/testing laboratory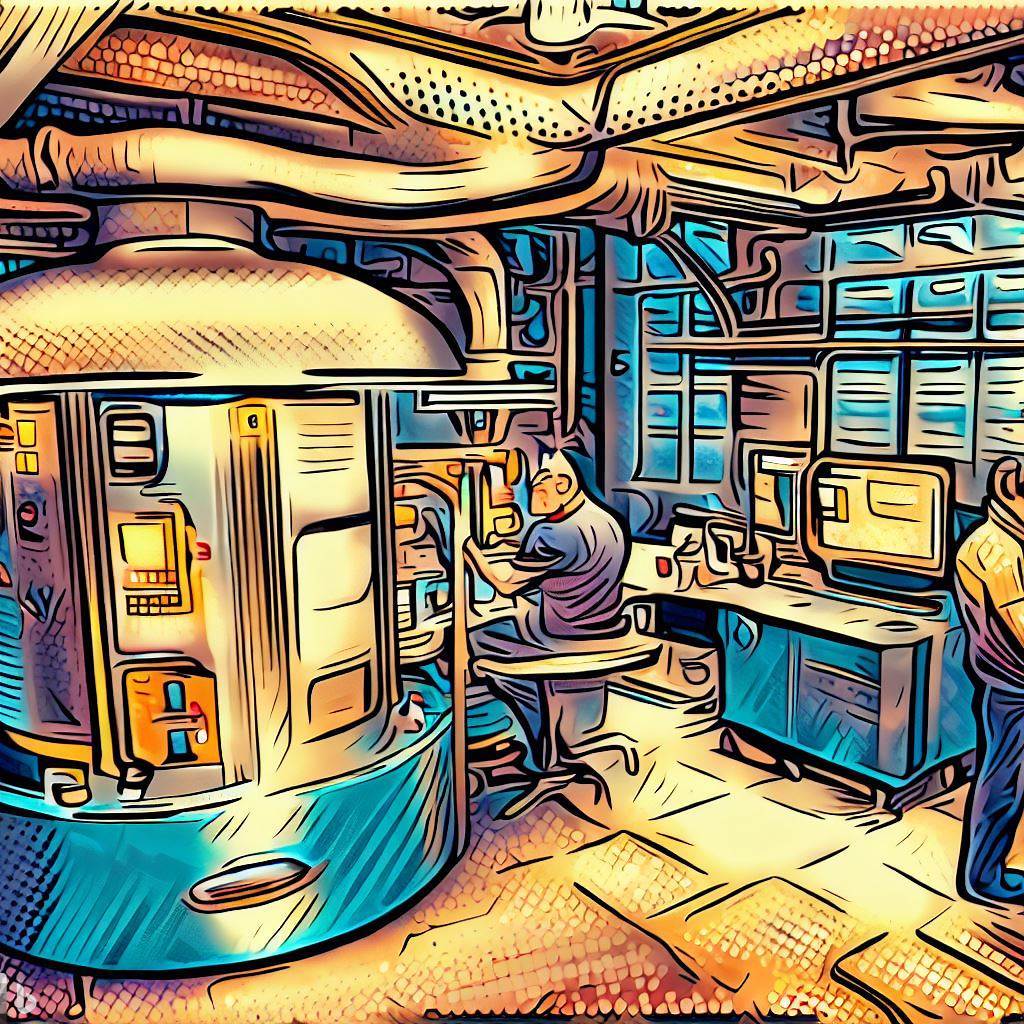
This is a quite manageable step, whether you are starting from scratch, or at adapting your lab when coming from ELISA or Microarray development. Testing and development of lateral flow tests requires no high-sophisticated lab setup.
- A lab bench with a set of pipettes might be already enough depending on your product idea.
- A reader to analyze your LF runs is a plus. This can be a very simple setup like a smartphone with a suitable holder and ideally a good light source, or a digital camera. You can also use a document scanner (Flatbed). Or you can use a specialized LF reader. Please see my article about LF readers [here]. LINK
- You might also want to have a small drying chamber.
- When you don’t have a good control and monitoring of your temperature and humidity in the lab already, then you might also want to have a small compartment for constant humidity and/or temperature.
- Lab equipment for making detection particle conjugates, antibody solutions, and buffers – or purchase all of those at the respective service suppliers. There will be a separate article about those.
“The design of the lateral flow test is a critical factor in its performance and reliability.”
All other equipment for making LF tests can be hijacked from your lateral flow test production.
2. Setting up manufacturing
So what equipment is needed for the LF manufacturing itself. Well, there are the following possible levels of using (semi-)automated equipment:
1. Zero automated = full manual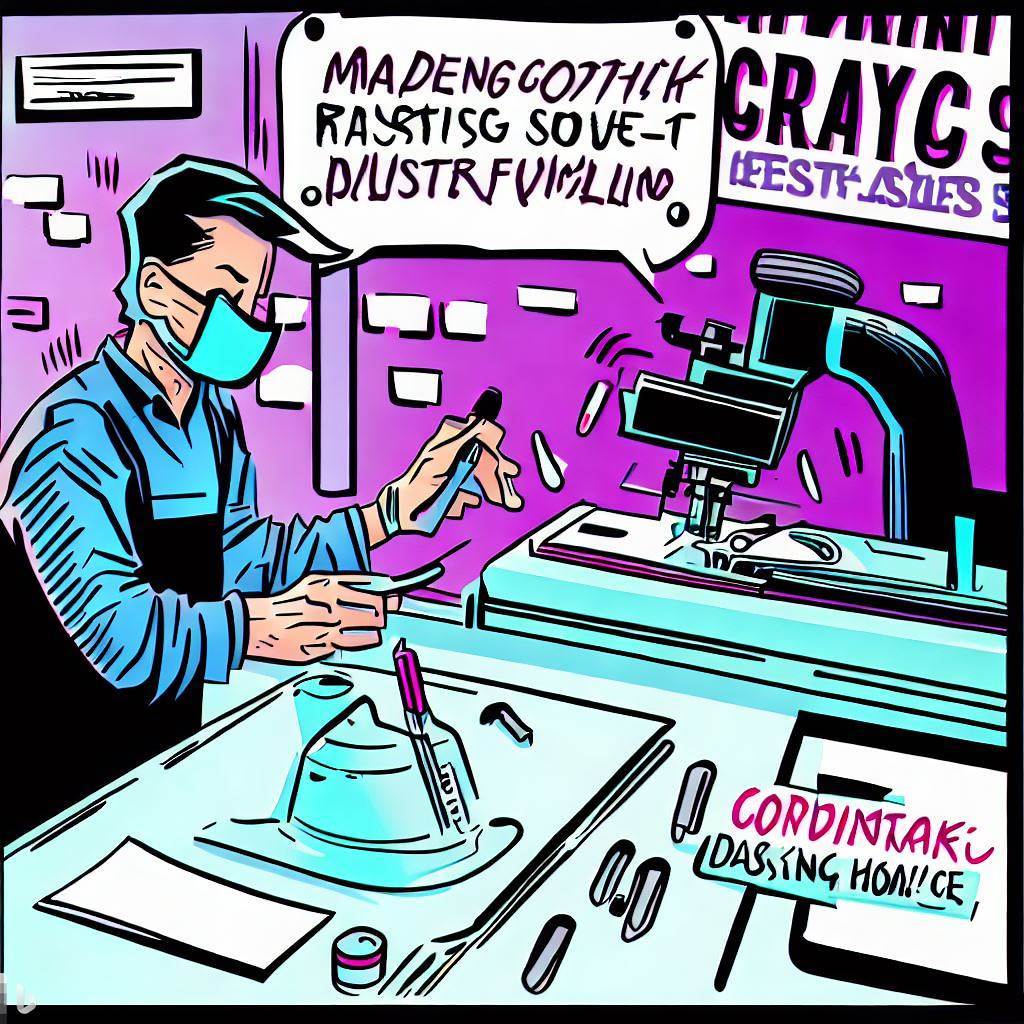
- In principle, each and every step of LF manufacturing can be performed manually.
- Cutting of pads, or nitrocellulose with an office paper cutter
- And/or Purchasing precut material (pads, nitrocellulose (NC) on backing card)
- Appling detection conjugate (i.e. for example gold nanoparticle with detection antibody) with pipette or dipping into solution and drying
- Applying capture antibody onto NC via pipette
- Assembly of the pad materials (sample/conjugate/waste) onto the NC backing card
- Cutting of single strips form the assembled card
- If necessary: application of cover tape
- If necessary: assembly of strips into cassette or storage in containers
- If necessary: Pouching of strips in premade (aluminum) pouches and sealing with a hot sealer.
Although I would not recommend this setup, at least not for the conjugate pad and NC step.
2. Minimal tech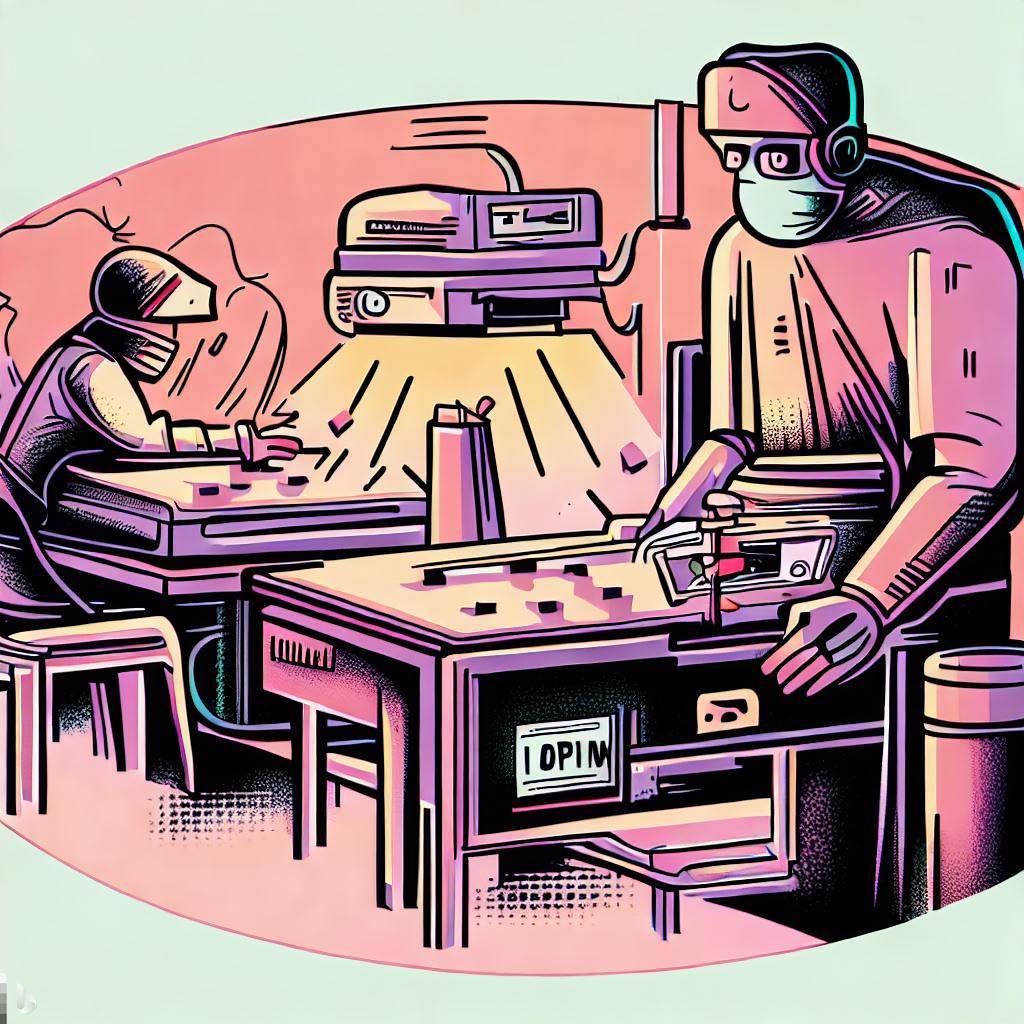
- To have a consistent and better controllable process you should invest in a dispensing unit. With this machine you can dispense the capture antibody on the NC but also the detection conjugate onto the conjugate pad. There are several well established manufacturers for those machines available – so no real need for homemade experiments. Albeit this comfort and control comes at a price of several thousand to several tensof thousands of euros – depending on your required level of quality and throughput.
Those dispensers will probably be the cornerstone of your manufacturing for a long time.
All other steps from point 1) can be done manually – if necessary.
Besides, I really recommend the following setup.
3. Minimal automated
Beside the dispensing units from point 2) you would want to have
- A laminator – at least a dedicated equipment like a Clam Shell Nest or a Universal Laminator. This ensures reproducible overlap of all materials on your strip and consistent layout which is of high importance to achieve dependable results.
Again, an invest of several thousand euros.
- A cutter for the LF cards. You really want to have a consistent strip width if you are applying the strip in cassette but of course also when you are using a dipstick LF. Everything other than that is not professional. There are two major cutter-types on the market: Guillotine Cutters working with one up- and down moving blade, and rotary cutters that work like office paper shredders, in principle. Depending on throughput and quality of the machines you are again facing to invest some thousand to ten-thousand euros.
- Nice to have at this stage:
- A drying/curing cabinet for conjugate pad/dispensed NC/strips ► 10 000 €
- If you are using cassettes: an assembly roller with a conveyor belt ► some thousand euros.
- If you are sealing aluminum pouches: a moving belt hot sealer
All the nice to have ones can again be the working horses for your development and manufacturing for a long time.
4. Medium automated
For this setup I assume that you are moving from a card-to-card manufacturing to a reel-to-reel manufacturing. That is, dispensing the NC on rolls, continuous drying and – complementary – also assembly of backing and pads in roll format. This requires: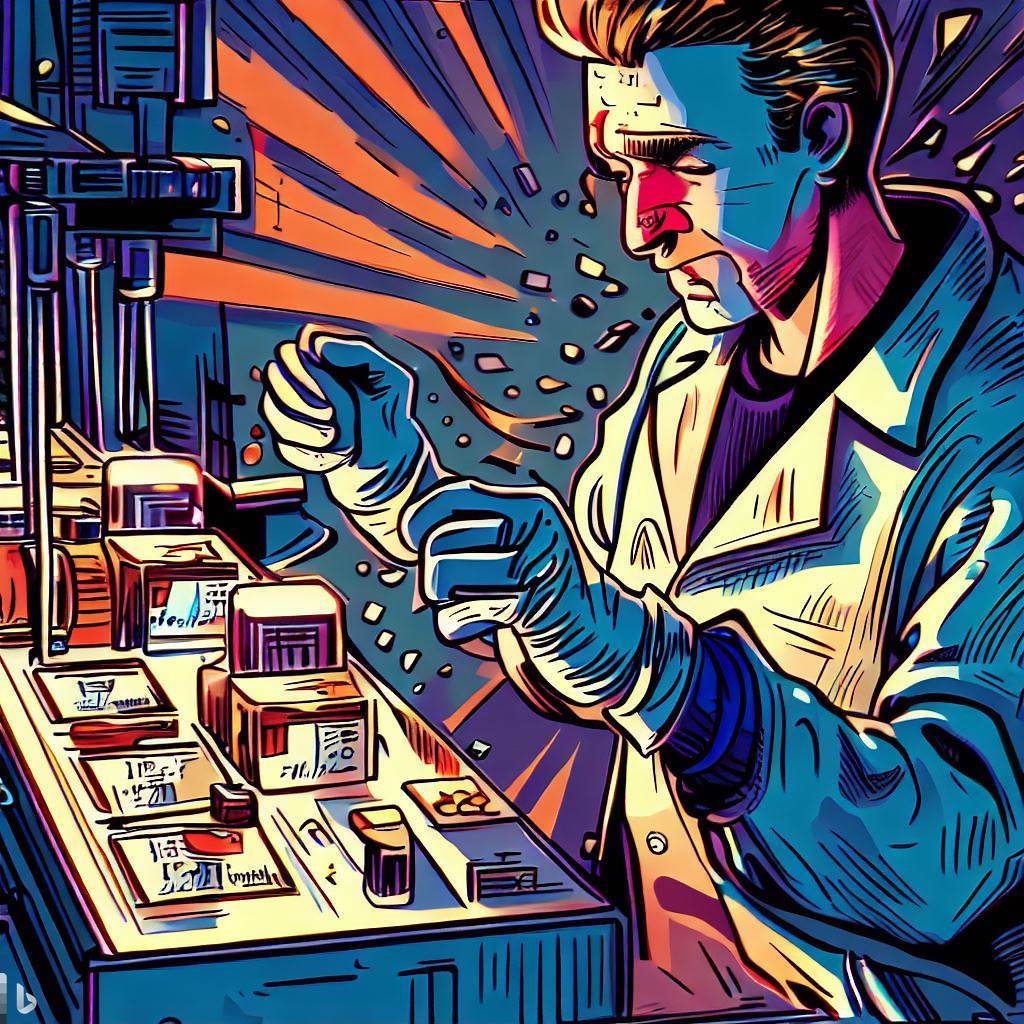
- A reel-to-reel dispenser with in-line drying tower(s). Costs: several hundred thousand euros.
- A reel-to-reel or reel-to-card laminator. Costs: again: several hundred thousand euros.
- Nice to have:
- Semi-automated printing or labeling ► some thousand euros.
That moves you from an output of a mere 10 000 tests to some 100 000 tests per month. But you are not only gaining more tests in a shorter time but also higher quality of your tests – as alignment of material, dispensed volumes, drying times, errors, etc. is constantly monitored and controlled by the machines. Your bottleneck will at this stage be then the assembly of strips in cassette and the pouching of the tests. This might be still manageable with more hands to work the semi manual processes.
5. High degree of automatization
This is the holy grail for every LF manufacturer as at this point you have the least amount of personnel costs per test and the highest output with the best quality. At this stage you are: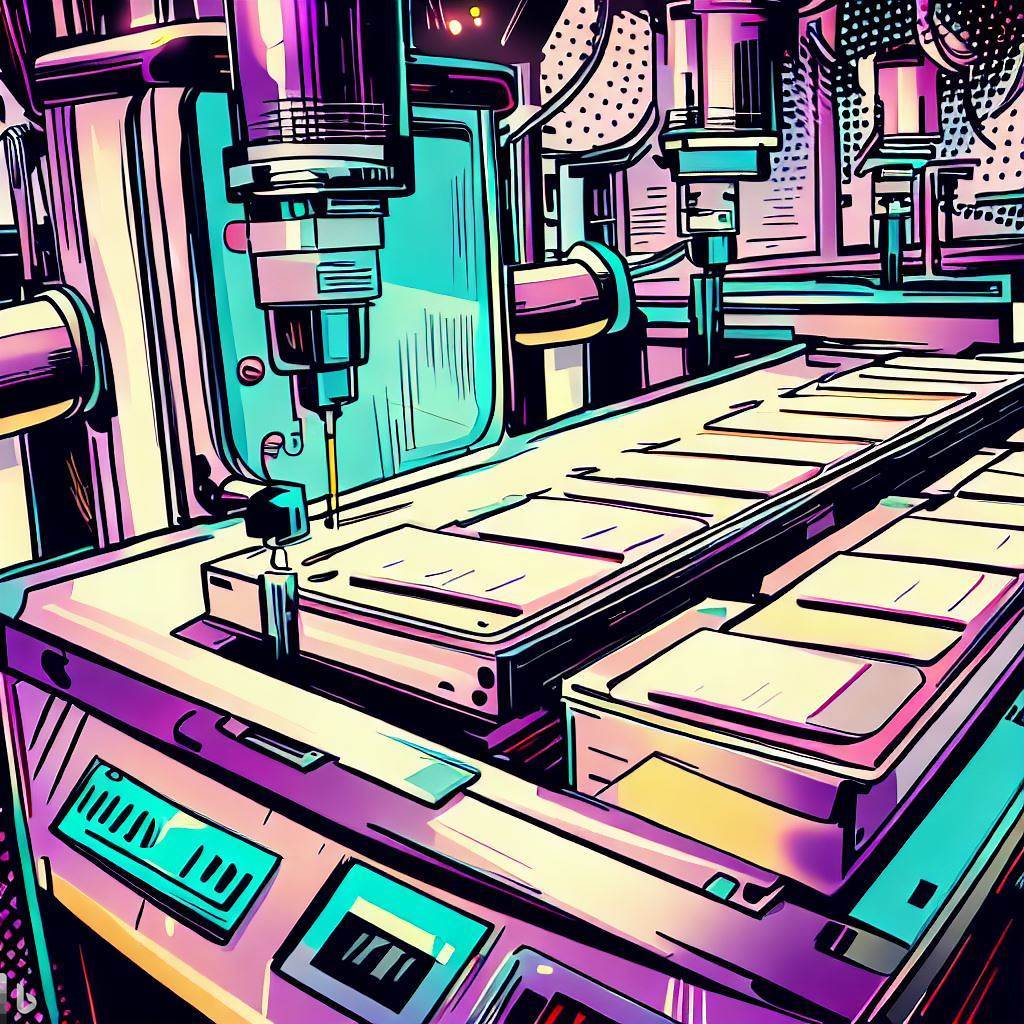
- Upgrading your reelto-card laminator to a reel-to-reel laminator: several ten thousand euros
- Reel feed cassette assembler that also labels your cassettes. There are several manufacturers active in the market with different level of application of robotic manipulators => several hundred thousand euros
- Pouching machine. Either a full automatic machine working with premade pouches or a tubular bag forming machine with in-line printing of the pouches.
That leaves at the end only the kit assembly (putting all kit components, i.e. pouch, dropper bottles, IFU, pipettes, and other small items) to the kit carton.
And this is only a short summary of the topic “equipment”. As you can see, the investment even in a small decent LF manufacturing unit will eventually sum up to a few hundred thousand euros. I have not mentioned that you will need in addition:
- Some space for the manufacturing equipment.
- Controlled and monitored room conditions.
- Storage space for raw, intermediate- and final goods with probably different temperature levels.
Do not forget: "Quality control is a crucial aspect of lateral flow test manufacturing, ensuring that each test meets the required standards." And it also costs money!
Of course you will need to hire skilled personnel to design, develop, and manufacture the tests. This will inevitably also reach a sum of several hundred thousand euros depending on the scale you are thinking about.
In-house manufacturing ensures a high degree of control over the entire process, from the initial concept to the final product. You can directly oversee every stage, from the selection of raw materials to the design of the test, ensuring that the final product meets your specific requirements.
Confidentiality and intellectual property generation and protection in lateral flow tests are other significant benefits of an in-house approach.
Furthermore, an in-house unit offers flexibility and adaptability. You can quickly implement changes in the design or manufacturing process, experiment with new ideas, and adapt to evolving market needs or regulatory requirements.
However, building an in-house unit also comes with its challenges. The initial investment can be substantial – as I have outlined above. Covering the cost of setting up the laboratory, procuring equipment, and hiring skilled personnel. Additionally, maintaining the unit involves ongoing costs such as salaries, maintenance, and quality control. Furthermore, if you are starting from scratch you will maybe underestimate the costs for setting up a quality management system, training of personnel, qualification, validation and documentation.
The need for expertise and skilled personnel is another significant consideration. Developing and manufacturing lateral flow tests require specialized knowledge and skills, and finding the right talent can be time-consuming and costly.
Regulatory hurdles are another challenge. The development and manufacturing of lateral flow tests are subject to stringent regulations to ensure safety and efficacy. Navigating these regulations requires expertise and can be a complex and lengthy process.
Despite these challenges, many organizations have successfully built in-house units. For instance, and just to name a few, Amodia has established a robust in-house development and manufacturing unit for lateral flow tests, enabling it to deliver high-quality products that meet specific market needs. Similarly, R-Biopharm has successfully developed various lateral flow assays in-house, demonstrating the feasibility and potential benefits of this approach.
In conclusion, here some of the advantages and challenges building an in-house development and manufacturing unit for lateral flow tests:
Advantages
|
Challenges
|
Complete control over the process
|
High initial investment
|
Confidentiality and intellectual property protection
|
Need for expertise and skilled personnel
|
Flexibility and adaptability
|
Regulatory hurdles
|
References
[1]: [Amodia's Lateral-Flow Dipstick (LFD)](https://www.amodia.de/index.php/en/technologies/17-lateral-flow-dipstick-lfd)
[2]: [R-Biopharm's Lateral Flow Assays](https://food.r-biopharm.com/technologies/lateral-flow-assays/)
3. Hiring a Custom Developer or Contract Manufacturer
Hiring a custom developer or contract manufacturer (CDMO) for diagnostic tests is an alternative to building an in-house unit. This strategy involves partnering with a specialized company that has the expertise and infrastructure to design, develop, and manufacture lateral flow tests on your behalf. As a former head of such a unit, I aim to provide valuable advice in this section.
One of the main advantages of this approach is the lower initial investment. Instead of investing in a laboratory, equipment, and personnel, you pay for the services of the CDMO. This can be a more cost-effective option, especially for small companies or startups.
Another advantage is access to established expertise and infrastructure. Custom developers and contract manufacturers have the knowledge, skills, and facilities to develop and manufacture lateral flow tests. They are familiar with the regulatory landscape and have established quality management and quality control procedures, which can potentially lead to a faster time to market than if you were to establish the complete setup by yourself.
However, hiring a CDMO also has its drawbacks. One of the main challenges is the reduced control over the process. While you can specify your requirements and expectations, the actual development and manufacturing process is in the hands of the service provider. It is your responsibility at every step to check and control your CDMO. Make it clear from the start who is in the driver's seat.
You should visit your CDMO’s facility before signing any contract. Let them guide you through all necessary processes and have a glimpse at SOPs, documentation, and of course, equipment. Also, take time to ask about the likely project leader, lab workers, etc., and ask about the number of people planned to work on the project. Based on this information, do your calculations and homework thoroughly.
Another point not to underestimate is that you are still going to invest a sum of several hundred thousand euros over time to get your product market-ready. And you really want to have control over this investment. But you also have to accept that external work costs money and that you might only see a fraction of the work you pay for at the CDMO. You are free to ask how your money is used.
Potential issues with confidentiality and intellectual property can also arise. While most service providers have measures in place to protect their clients' proprietary information, the risk of leaks or misuse cannot be completely eliminated. A contract controlling background and foreground knowledge, inventions, and cases of information breach should be in place early on.
You should get a clear view and understanding of the processes and document landscape at your CDMO, so you can adapt to it. If you try to establish your processes at the CDMO, you will lose efficiency. Remember, one of the reasons to go to the CDMO was that you could rely on already established processes.
Note that a good CDMO sees product development and/or manufacturing not only as a service. The CDMO will eventually identify with the product and establish a strong commitment – this can be beneficial for you, but also be a cause for friction over time. Be clear in your visions and communication and show appreciation for the effort of the CDMO.
Management of your CDMO will cost you additional time and money. You want to make sure that you always get the full picture. Set up a communication and reporting framework early in the process. Weekly short and focused team meetings will ensure that you stay on top of information and control. See your CDMO as a remotely working team member. Plan for in-person visits (not audits!) quarterly. You should also demand or set up a tight net of milestones. If possible and meaningful, also invite your CDMO to your site regularly. Forge strong bonds to establish trust – you will need this in the long term.
Dependence on the service provider is another challenge. If the service provider encounters problems or goes out of business, it can disrupt your supply chain and delay your product launch.
Despite these challenges, many organizations have successfully collaborated with custom developers or contract manufacturers. It is not rocket science to find a CDMO, but it is an important task to identify an excellent CDMO that fits you.
- You are going to give a decent amount of money to the CDMO
- You will work probably for years with this CDMO – fit of culture and sharing the same values is important
- Your business, i.e. delivery of sellable product relies fully on the CDMO – but your CDMO might not solely rely on you. There will inevitably be other customers, other priorities, changing targets over time.
- Changing CDMOs is always a very tedious process – independent of the stage of the development/manufacturing and should be avoided.
In conclusion, utilizing custom development or contract manufacturing for lateral flow tests offers several advantages, including lower initial investment and access to established expertise and infrastructure. However, it also involves challenges such as less control over the process, potential issues with confidentiality and intellectual property, and dependence on the service provider.
Advantages
|
Challenges
|
Lower initial investment
|
Reduced control over the process
|
Access to established expertise and infrastructure
|
Potential issues with confidentiality and intellectual property
|
Faster time to market
|
Dependence on the service provider
|
Cost-effectiveness
|
Risk of service disruption
|
Access to specialized knowledge and skills
|
Need for constant monitoring and control
|
4. Making the Decision
Deciding between building an in-house unit and hiring a custom developer or contract manufacturer for lateral flow tests is a critical strategic decision. It requires careful consideration of various factors, including your budget, timeframe, in-house expertise, and long-term goals. This section provides a simplified guide to give you a starting point. However, this inevitably has to be adapted to your specific background and challenge.
- Budget: Building an in-house unit requires a significant initial investment, while hiring a custom developer or contract
manufacturer involves ongoing costs. You need to consider your financial resources and how much you are willing to invest.
- Timeframe: The timeframe is another important consideration. Building an in-house unit can be a lengthy process, while hiring a custom developer or contract manufacturer can potentially lead to a faster time to market.
- In-house Expertise: The level of in-house expertise is a critical factor. If you have the necessary skills and knowledge in-house, building your own unit might be a viable option. However, if you lack the necessary expertise, hiring a custom developer or contract manufacturer can provide access to established knowledge and skills.
- Long-term Goals: Your long-term goals should also influence your decision. If you aim to control the entire process and protect your intellectual property, building an in-house unit might be the best choice. However, if your goal is to quickly bring a product to market with a lower initial investment, hiring a custom developer or contract manufacturer might be more suitable.
Here is a decision-making flow scheme to help guide your decision:
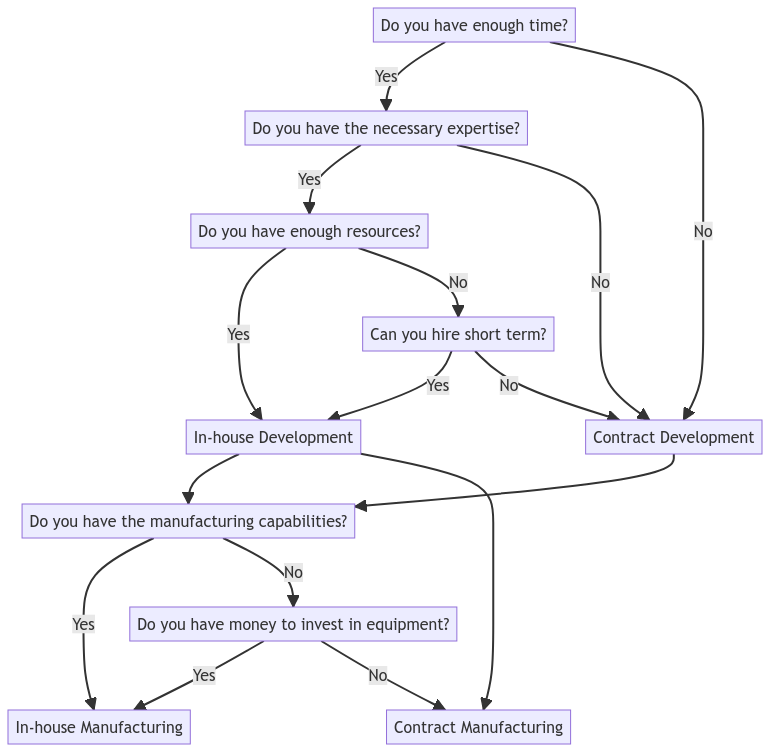
In conclusion, the decision between building an in-house unit and hiring a custom developer or contract manufacturer for lateral flow tests depends on various factors, including your budget, timeframe, in-house expertise, and long-term goals. Conducting a thorough cost-benefit analysis can help you make an informed decision that aligns with your strategic objectives. Hiring a lateral flow test consultancy can provide valuable guidance and expertise in the development and manufacturing process.
5: How Consultants Can Help
The lateral flow landscape has to offer a wide panorama. It's a field filled with complexities and nuances and can be a labyrinth of decisions that can make or break your venture. Whether you're considering setting up your own in-house unit or thinking of hiring a CDMO, there are several challenges waiting for you on the way. But you are not alone on your journey.
As the former head of a CDMO unit, I've seen the ins and outs of the lateral flow industry. I've walked the walk with startups and established companies alike, guiding them through the maze of lateral flow test development and manufacturing.
My consulting services are tailored to your specific challenge and needs. I'll help you conduct a thorough cost-benefit analysis, evaluate your in-house capabilities, and assess potential service providers. I can support you on your supply chain, regulatory compliance, quality control, and intellectual property protection.
Conclusion
In this article, we've explored the two main paths to developing and manufacturing lateral flow tests: building an in-house unit and hiring a custom developer or contract manufacturer. Each approach has its own unique advantages and challenges:
- Building an in-house unit offers complete control over the process, confidentiality, and intellectual property protection, flexibility, and adaptability. However, it requires a high initial investment, expertise and skilled personnel, and navigating regulatory hurdles.
- Hiring a custom developer or contract manufacturer provides a lower initial investment, access to established expertise and infrastructure, potentially faster time to market, and cost-effectiveness. Yet, it comes with reduced control over the process, potential issues with confidentiality and intellectual property, dependence on the service provider, and the need for constant monitoring and control.
Your decision should be based on various factors, including your budget, timeframe, in-house expertise, and long-term goals. Conducting a thorough cost-benefit analysis can help you make an informed decision that aligns with your strategic objectives.
Remember, you don't have to navigate this complex landscape alone. As a consultant with extensive experience in the lateral flow industry, I can provide valuable guidance and support, helping you to:
- Conduct a thorough cost-benefit analysis
- Evaluate your in-house capabilities
- Assess potential service providers
- Navigate supply chain, regulatory compliance, quality control, and intellectual property protection
If you need further assistance or consultation, don't hesitate to reach out to me. Whether you're just starting out or looking to fine-tune your existing processes, I'm here to help. Let's walk this path together.
Don’t hesitate to contact me and book a meeting.
Share your own experiences, ideas, or challenges related to lateral flow test development and manufacturing and send me a message.
Disclaimer: All pictures in this article where produced with the help of BING Image Creator.