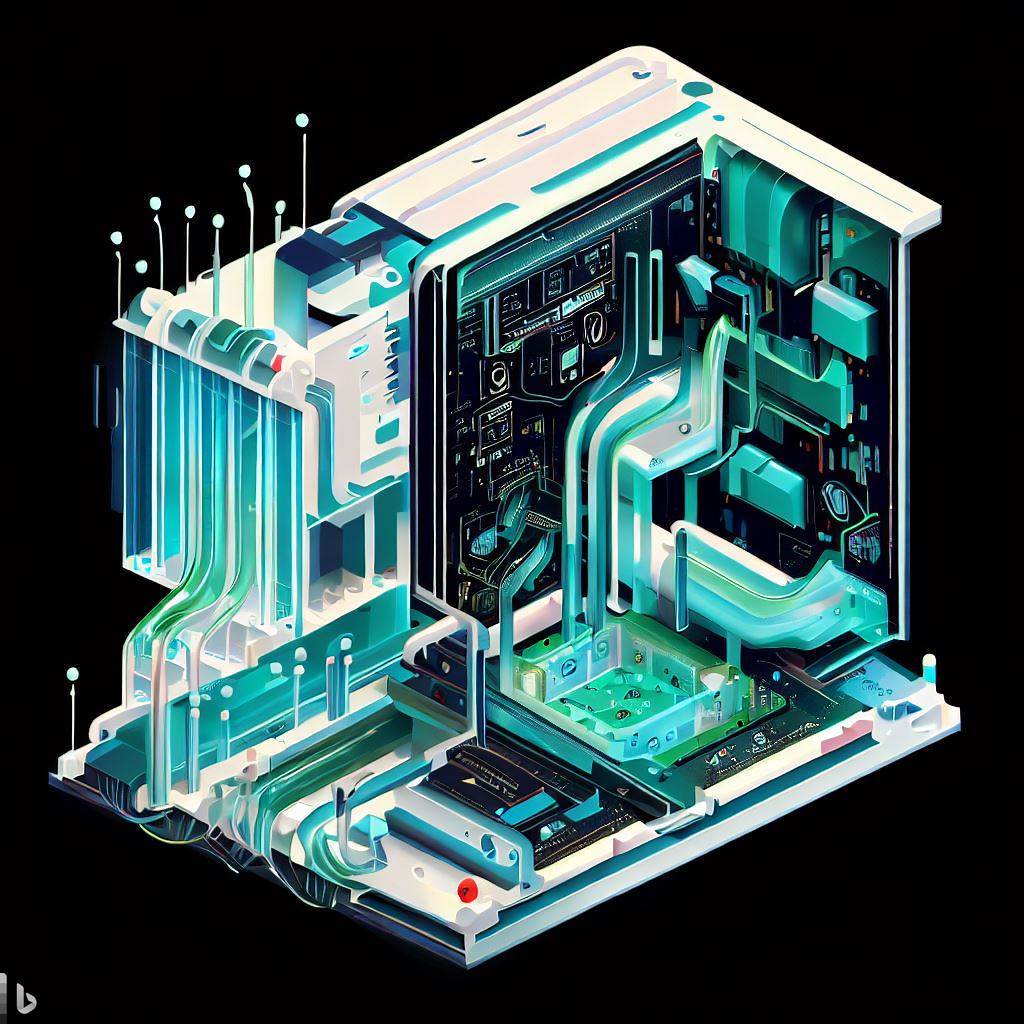
Guide to Cassette Selection or Design for Lateral Flow Test Development and Manufacturing - Part 2
Introduction
Imagine holding the key to significantly enhancing the performance, reliability, and usability of lateral flow tests. That key is the cassette - the protective housing that not only safeguards the test strip but also provides a user-friendly interface for sample application, result interpretation, and data capture. The right cassette selection or design can be a game-changer, and even the exterior design can be leveraged to create brand awareness for your lateral flow tests. However, it's worth noting that a unique exterior design might pose challenges at your CDMO if it doesn't align with standard processes and available equipment.
If you're keen on delving into the intricacies of cassette selection and design for lateral flow tests, you've come to the right place. Whether you're seeking a suitable cassette for your specific test as a potential customer, aiming to optimize your cassette design as a professional in the field, or simply a student wanting to grasp the fundamentals of cassette engineering, this blog post is tailor-made for you. Within these pages, we will provide you with valuable insights, tips, and expert guidance.
In this second part of our guide, we will focus on
- the design and optimization of lateral flow test cassettes,
- the principles of Design for Assembly (DFA)
- the importance of exterior design in branding and,
- trends in cassette design.
This part is especially beneficial for professionals in the field looking to enhance their cassette design and staying up to date in lateral flow test development.
1. Design Aspects
1.1 Overview of Materials Commonly Used in Cassette Construction
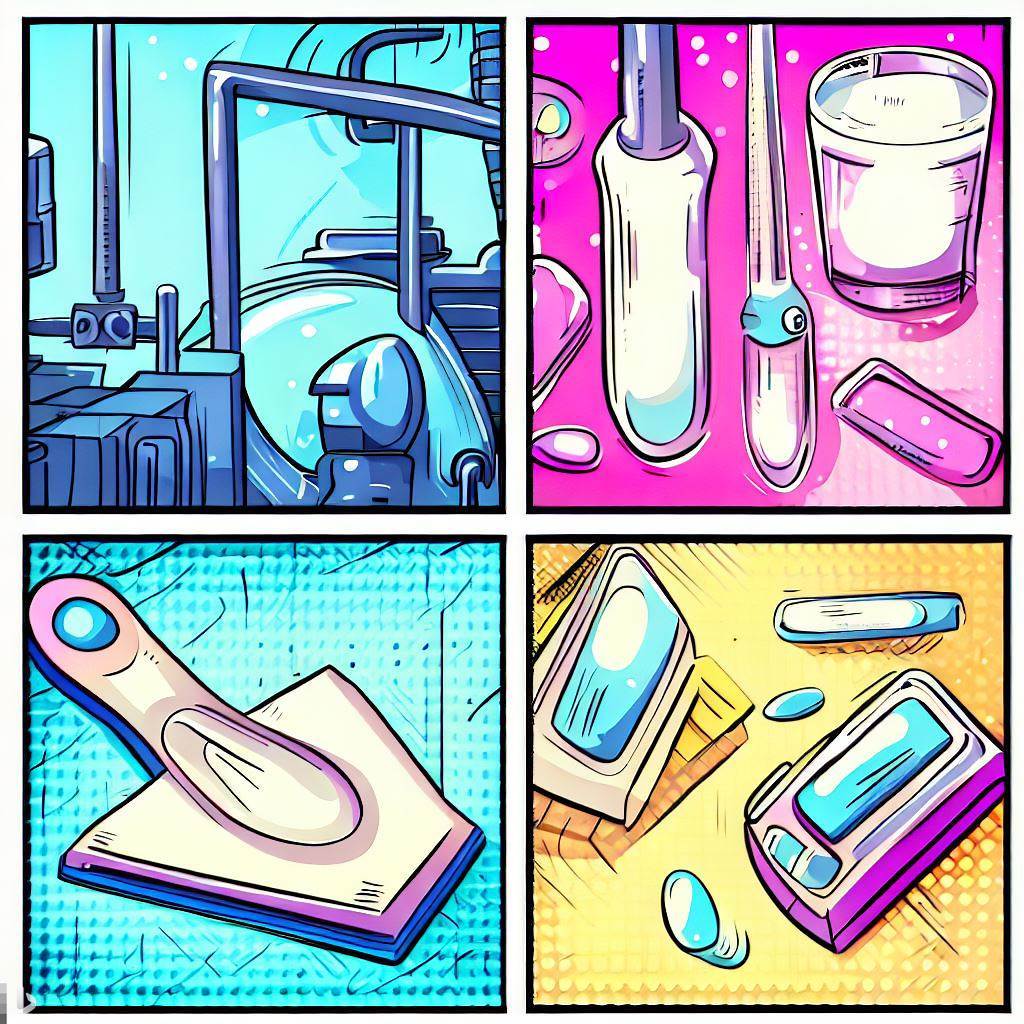
Different types of plastics or plastic mixtures are employed for cassette manufacturing, each with unique properties and advantages.
- Polystyrene (PS): Known for its excellent optical clarity, PS is a cost-effective choice for cassette manufacturing, facilitating result visualization. It can be easily applied using injection molding techniques, and additives can be incorporated to enhance optical properties.
- Polypropylene (PP): PP offers good chemical resistance and high structural integrity, making it suitable for holding samples and reagents. It can be manufactured through injection molding or laser cutting processes, and additives like carbon black can be added to improve light-blocking properties.
- Acrylonitrile Butadiene Styrene (ABS): ABS is a thermoplastic known for its strength, impact resistance, and dimensional stability. It is commonly used in cassette components requiring robust mechanical properties. ABS can be easily molded, allowing for complex cassette designs.
- Polylactic Acid (PLA): PLA is a biodegradable and bio-based plastic derived from renewable resources like cornstarch or sugarcane. It offers a sustainable alternative to conventional plastics. PLA cassettes can be manufactured using 3D printing techniques, providing flexibility in design customization. However, PLA may require additional coating or treatment to enhance its moisture resistance properties. Nowadays, PLA is not widely employed in cassette manufacturing but prototyping.
- Sustainable Plastic Blends: Some manufacturers have developed plastic blends that incorporate recycled or bio-based materials. These blends aim to reduce environmental impact and improve sustainability. For example, a mixture of PLA and polyethylene terephthalate (PET) can offer enhanced mechanical properties while utilizing renewable resources.
It is noteworthy, that various additives can be incorporated into plastic formulations to improve cassette functionality. For instance, laser-markable additives can enable precise marking of identification codes or lot numbers on cassettes. Colorants can be used to differentiate between different cassette types or indicate specific test parameters.
1.2. Recent Developments in Sustainable Cassette Materials
Conventional LFTs generate significant plastic waste, as they typically use plastic cassettes to house the test strips and protect them from
environmental factors.
“Did you know that according to the International Solid Waste Association (ISWA), during COVID-19 pandemic probably an increase of about 300% in single-use plastics is to be estimated? Furthermore, every single time that a COVID-19 lateral flow test is used, 10 grams of plastics are disposed into the environment.”
Recent developments have focused on finding sustainable alternatives for LFT cassettes that are biodegradable, compostable, or recyclable. Here are some examples of these materials:
- Gelassette: A novel LFT cassette made of gelatin, a natural polymer derived from animal collagen. Gelatin mimics the properties of plastic, such as flexibility, transparency, and water resistance, but it is also fully biodegradable in soil and water. Gelassette can be used for COVID-19 testing or any other single-use testing that requires a lateral flow assay.
- PLA (polylactic acid) and blends: PLA has similar characteristics to conventional plastics, such as strength, durability, and clarity, but it is also biodegradable under industrial composting conditions. PLA can be used to make LFT cassettes that are compatible with various labels and reagents and manufacturing processes. Blends of PLA and a new types of polyester can potentially be composted at home.
- Cardboard: A paper-based material that is widely available, cheap, and recyclable. Cardboard can be used to make LFT cassettes that are sturdy, lightweight, and easy to handle. Cardboard can also be coated with different materials to enhance its water resistance, optical properties, and biocompatibility. Cardboard can be printed.
These examples illustrate some of the recent advances in sustainable cassette materials for LFT development and manufacturing. By adopting these materials, LFTs can become eco-friendlier and socially responsible devices that meet the growing demand for point-of-care diagnostics and other applications.
In addition to these, there are ongoing research efforts to develop new materials and technologies for LFT cassettes. For instance, a recent study has reported the development of a new type of biodegradable plastic that can be used for LFT cassettes.
References:
[1] [Vitrosens] (https://vitrosens.com/what-are-sustainable-alternative-materials-for-biodegradable-rapid-test-kit-cassette/).
[2] [Surescreen] (https://surescreen.net.au/surescreen-to-mass-produce-world-first-biodegradable-covid-test%EF%BF%BC/).
[3] [Cambridge Design] (https://www.cambridge-design.com/blog/how-to-reduce-the-carbon-footprint-and-plastic-waste-of-lfts/).
[3] [Gelassette] (https://www.gelassette.com/).
[4] https://www.dezeen.com/2022/05/20/covid-19-test-morrama-recyclable-biodegradable-design/.
[5] https://www.ncbi.nlm.nih.gov/pmc/articles/PMC8600310/ .
[6] https://pubs.rsc.org/en/content/articlehtml/2022/lc/d2lc00380e.
[7] https://www.nature.com/articles/s41578-021-00407-8.
[8] https://www.mdpi.com/2073-4360/15/5/1184.
1.3. Importance of Fluid Flow Control in Lateral Flow Test Cassettes
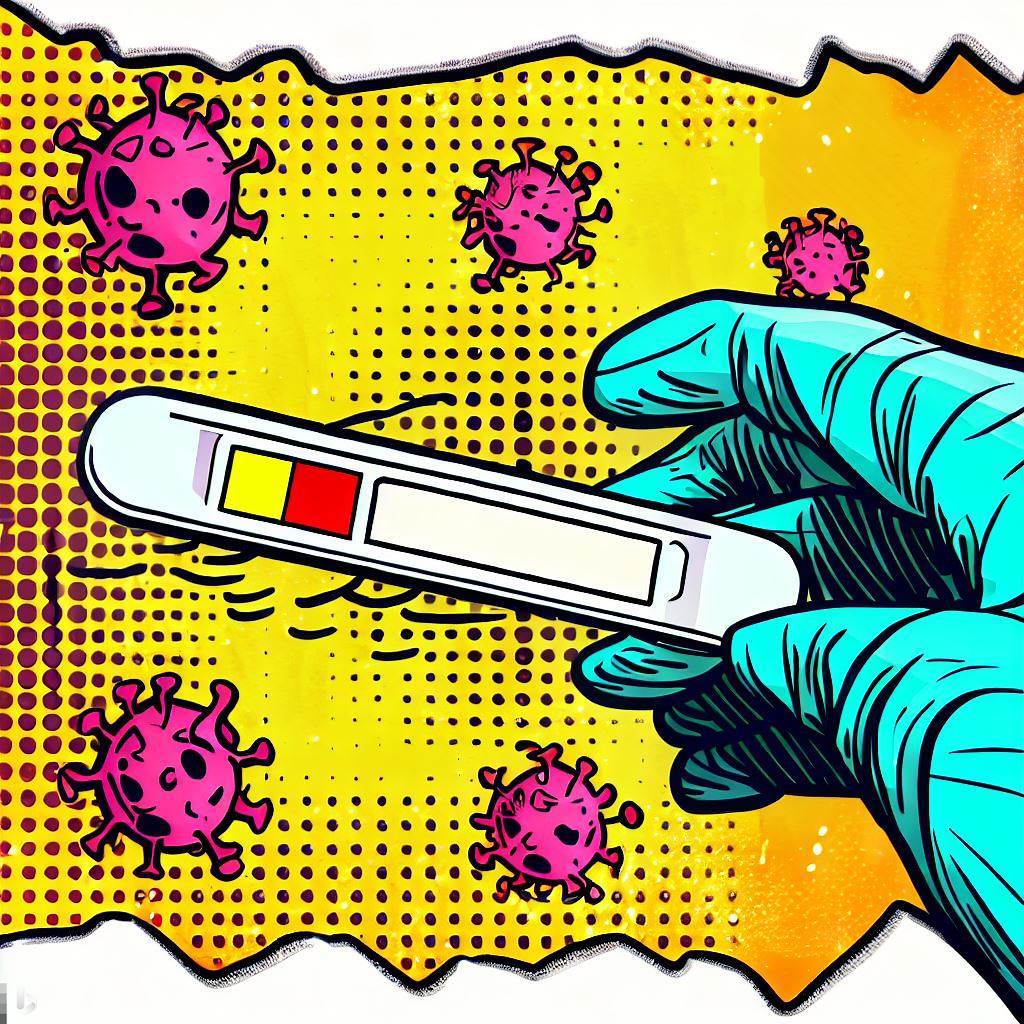
The control of fluid flow within lateral flow test (LFT) cassettes is a core aspect of assay performance. The movement of the sample and reagents through the test strip must be carefully managed to ensure accurate and reliable results. This involves the precise control of fluid velocity, volume, and direction, which can significantly influence the sensitivity, specificity, and speed of the test. The fluid flow control mechanisms in LFT cassettes are designed to facilitate capillary action, maintain optimal hydration of the test strip, and prevent backflow or leakage. These mechanisms are integral to the proper functioning of the test, affecting the interaction between the analyte and the detection reagents, the clarity of the test line, and the overall user experience.
Designing an LFT cassette for optimal fluid flow involves several key considerations:
- Capillary action is the primary driving force for fluid movement in LFTs. The design of the cassette should facilitate and not prevent this phenomenon by ensuring close contact between the single materials in contact with the liquid (Sample-/conjugate pad/nitrocellulose/absorbent pad).
- Cavern Design: The design of cavities for the strip, overflowing sample or reagent solution, waste solution is oftimes neglected but of great importance for a smooth user experience.
- Drying/Wicking: The design must make sure during storage before use that the LF is constantly dry. But on the other hand, the design must make sure, that the LF once the sample is added has a constant humidity and sample doesn’t evaporate/dry during the assay.
“If the pressure points in the cassette are not matching the LF design you can clearly expect very undesired effects.”
1.4. Sample and Reagent Handling
Design Considerations for Sample and Reagent Loading and Containment
The design of lateral flow test cassettes must consider the efficient loading and containment of samples and reagents. The sample
application area should be designed to facilitate easy and accurate sample application, while minimizing the risk of contamination. The use of absorbent pads help to control the volume of the sample and ensure uniform distribution across the test strip. Nonetheless, the sample port – or in some cases also the sample valve – must be design in a way that
- The sample volume can be held and sample doesn’t overflow,
- The sample is completely transferred to the sample pad,
- Surface tension of the sample is regarded.
Reagent storage is another critical aspect of cassette design. The reagents used in lateral flow tests, such as antibody or antigen conjugates, must be stored in a stable and protected environment to maintain their (long term-) functionality. This often involves the use of desiccants or humidity control agents to prevent moisture-induced degradation. Some assay formats also incorporate already buffer or extraction solutions or contain lyophilized reagents within the cassette – and also those must be stored in a stable environment.
Challenges and Solutions Related to Sample Volume, Leakage Prevention, and Reagent Stability
One of the main challenges in cassette design is managing the sample volume. Too much sample can lead to oversaturation of the sample pad leading to undesired effects, while too little sample for example due to insufficient transfer from sample port to sample pad, may not trigger a detectable response. To address this, some cassette designs incorporate sample wells or chambers that can hold a precise volume of sample or have a geometry that enhances sample flow.
Leakage prevention is another important consideration. The cassette must be designed to contain the sample and reagents securely, without risk of leakage or cross-contamination. This can be achieved through the use of secure seals or barriers designed in the cassette itself, as well as careful material selection to ensure compatibility with the sample and reagents.
“During my time as head of lateral flow development and contract manufacturing we had one specific customer cassette that showed a very strange behavior in about 1 out of 10 runs. The sample (whole blood) was visible in those faulty runs on the membrane as a red smear – although a sample pad was used that should have filtered the red blood cells. After a long series of tests the team identified a randomly leaky sample port as cause. Sample was just flowing above the sample pad directly onto the membrane as it was adhering to the cassette top part due to its surface tension.”
Maintaining reagent stability is also a significant challenge in cassette selection or design. Reagents must be stored in a way that preserves their activity and prevents degradation over time.
References:
[1]: [Lateral Flow Assay Cassette Design | DCN Dx] (https://dcndx.com/blog/lateral-flow-assay-cassette-design/)
2. Design for Assembly and Automation
Design for Assembly (DFA) principles should be considered for selection and design of lateral flow test cassettes. DFA principles aim to simplify the design of the product to make it easier to assemble, thereby reducing assembly costs, increasing productivity, and improving
product quality and reliability. In the context of lateral flow test cassette manufacturing, DFA principles guide the integration of various components, ease of assembly, and compatibility with automation processes and equipment.
This enables for numerous benefits, including increased manufacturing speed, precision, and consistency, as well as reduced labor costs. However, it also presents challenges, such as possible limitations regarding outer design or usable components.
Several manufacturers offer more or less specialized machines for (semi-)automated cassette assembly. Most of them have only limited flexibility with regard to the form factor of the cassette and also flexibility with regard to simply switch between different cassette types. So the choice of the amount of different cassette designs will inevitably also influence the choice of machine you will use for assembly – the same is true vice versa.
But not only the exterior is important for DFA. Also the interior needs to be optimized for DFA. If you start with manual or semi-automated cassette assembly, you want to make sure that the operator knows where to put the strip and in which direction to put it. So it is wise to include optical as well as mechanical guiding in the strip slot and other places.
Additionally, also the choice of desiccant will influence your choice of cassette or assembly process. Why? Because if you are going to use standard drying packs, that are not assembled within the cassette but rather packed into the pouching, then you can use quite standard assembly machines and also the manual assembly process will be easier. However, if you are going to you drying pills - that may have other benefits not to be discussed here – then you have to plan for at least two inserting steps: 1) the strip (obviously) and 2) the drying pill. This results in 1) having a dedicated space in the cassette to securely store the pill and 2) having a dedicated (additional) process step (may be manual placement of the pill, maybe additional pick-and-place station in your assembly machine).
There are several excellent and readily available assembly machines on the market, but of course you can also have a look at getting a specially built machine for your specific requirements by a machine builder.
Suppliers to look for standard machines (no claim to completeness):
References:
[1] [Ginolis] (https://ginolis.com/)
[2] [Kinematic] (https://www.kinematic.com/)
[3] [Kinbio] (https://www.kinbio.com/)
[3] [Huxley Bertram - Lateral Flow Diagnostic Test Assembly] (https://huxleybertram.com/portfolio-item/lateral-flow-diagnostic-test-assembly/)
3. Recent Developments in All-in-One Lateral Flow Test Devices
A recent trend in the field of lateral flow test devices is the development of all-in-one devices. These devices integrate more or all the
necessary components for testing into a single, user-friendly platform, enhancing convenience and reducing the potential for user error.
- One such device is the Rapido Dx by Solios Diagnostics, which offers a rapid, portable solution for molecular diagnostics. It integrates sample preparation, amplification, and detection into a single device, making it a versatile tool for point-of-care testing.
- ReadyGo offer a range of diagnostic tests and tools designed for use at home, in labs, and beyond. Their tests are designed to be accessible, affordable, and accurate, with a focus on ease of use and lab-grade testing.
- Another interesting approach is Atomo's lateral flow cassette by Atomo Diagnostics, which offers a rapid, integrated solution for diagnostic testing. It combines the necessary components for testing, including lancets and pipettes, into a single device, making it a versatile tool for point-of-care and self-testing.
In addition to these specific examples, recent research and development efforts have led to the creation of other notable all-in-one lateral flow test devices.
These all-in-one devices offer several advantages, incl
uding convenience, ease of use, and the ability to provide rapid results. However, they also present potential challenges, such as ensuring the stability and effectiveness of the integrated components, and the need for rigorous validation to ensure accuracy and reliability.
Looking forward, the trend towards all-in-one lateral flow test devices is likely to continue, driven by the ongoing need for rapid, convenient, and accurate diagnostic testing. As technology continues to advance, we can expect to see further innovations in this field, potentially including devices capable of detecting a wider range of analytes, and devices that integrate advanced data analysis and reporting capabilities.
References:
[1] [Solios Diagnostics] (https://www.solios-dx.com/).
[2]: [ReadyGo](https://www.readygotest.com/).
[3] [Atmo Diagnostics] (https://www.atomodiagnostics.com/lateral-flow/).
Conclusion
In this second part of the guide, we've explored the different materials used in cassette construction, each with its unique properties and advantages. We've also highlighted the importance of fluid flow control, sample and reagent handling, and the principles of Design for Assembly (DFA) in lateral flow test cassettes. Furthermore, we've discussed the recent developments in sustainable cassette materials and all-in-one lateral flow test devices, which are shaping the future of lateral flow test development and manufacturing.
The right cassette selection or design can be a game-changer for your lateral flow tests. It not only safeguards the test strip but also provides a user-friendly interface for sample application, result interpretation, and data capture. Moreover, the exterior design can be leveraged to create brand awareness for your lateral flow tests.
Whether you're seeking a suitable cassette for your specific test, aiming to optimize your cassette design, or simply wanting to grasp the fundamentals of cassette engineering, I hope this guide has been beneficial. However, I understand that navigating the complexities of cassette selection and design can be challenging.
If you need further assistance or consultation, don't hesitate to reach out to me.
Don’t hesitate to contact me and book a meeting.
Share your own experiences, ideas, or challenges related to lateral flow test cassettes and send me a message.
Disclaimer: All Pictures and Sketches were produced by AI Bing Image Creator.