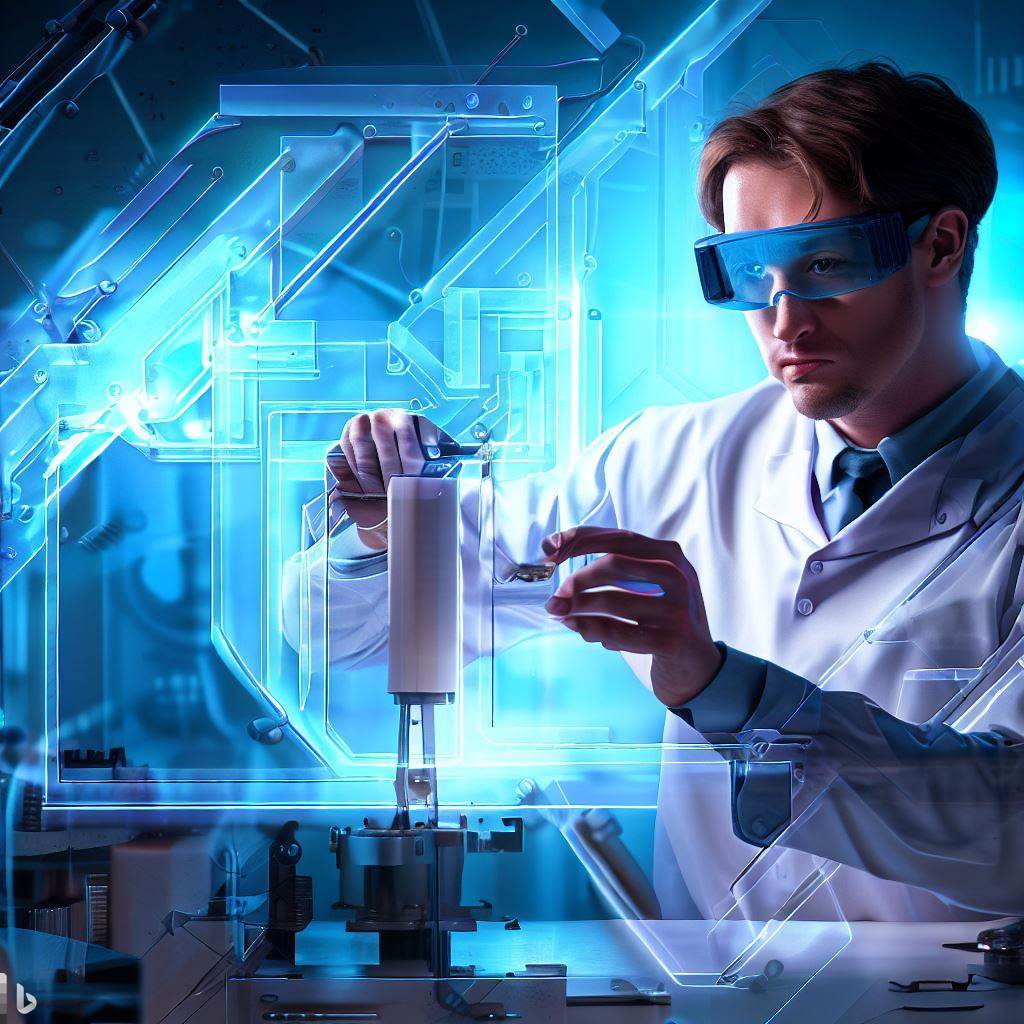
Overcoming Challenges in Developing and Manufacturing Lateral Flow Tests
Lateral flow tests have revolutionized medical diagnostics, environmental monitoring, and food safety with their simplicity, affordability, and rapid results. However, behind their seemingly effortless functionality lies a world of challenges in their development and manufacturing. In this article, we delve into the common obstacles encountered in the quest to create these medical tools, exploring the crucial steps to success and the innovation required to conquer the hurdles along the way.
From the initial transfer of ideas to the contract developer and manufacturer, to the critical choices of materials, including nanoparticles and antibodies, and the scale-up process and regulatory hurdles, we will navigate through the twists and turns of this scientific journey.
Whether you are a seasoned scientist, a lateral flow developer, an aspiring student, or a dedicated professional, this article will empower you with insights into the challenges faced in the development and manufacturing of lateral flow tests. I aim to provide you with a comprehensive understanding of the roadblocks that may lie ahead. Together, we can explore strategies and best practices to overcome these hurdles and enable the true potential of your lateral flow tests.
1. Transfer of Ideas from Customer to Contract Developer and Manufacturer
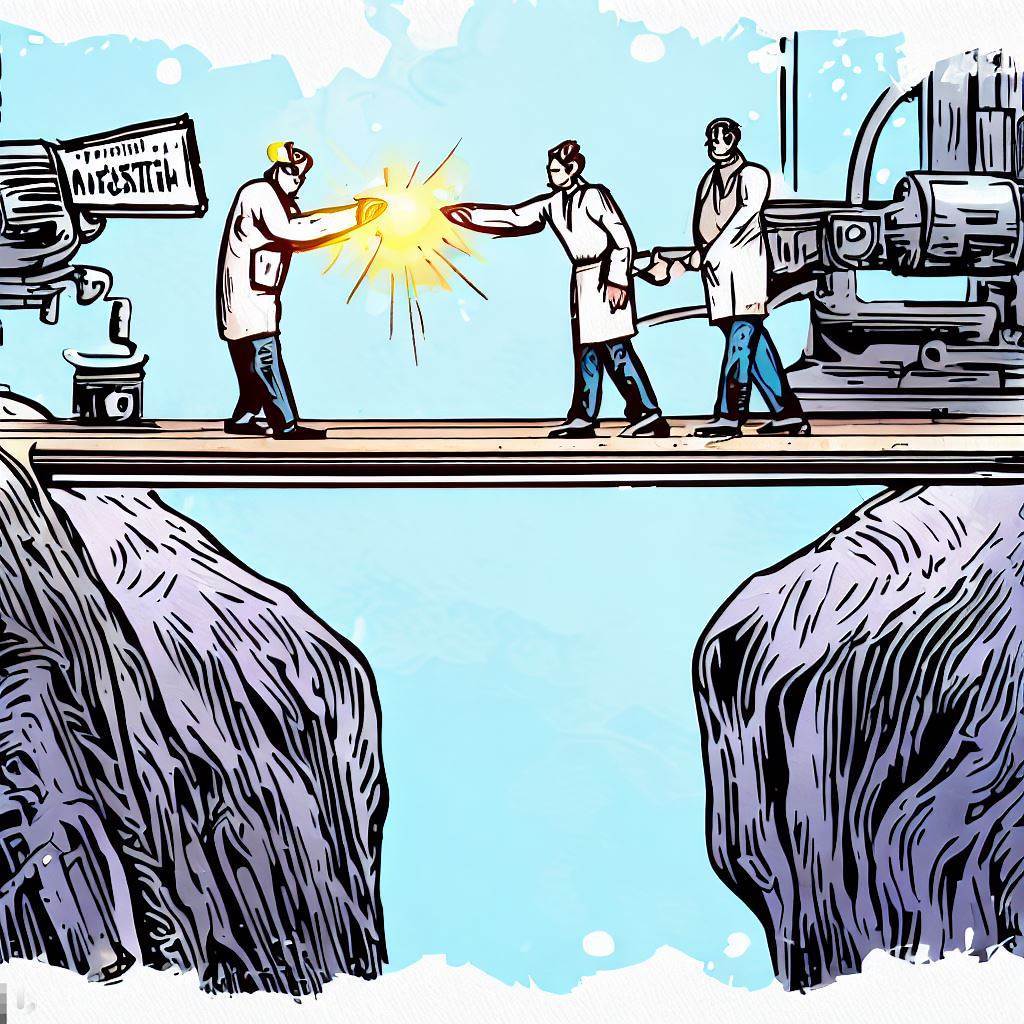
The journey of developing a successful lateral flow test begins with a seamless transfer of ideas from the customer to the contract developer and manufacturer. Clear and effective communication between the involved parties is crucial to ensure an extensive understanding of the test's intended purpose, target analyte, and performance specifications. However, bridging the gap between the customer's vision and the developer's expertise can be challenging.
In this intricate process, an experienced consultant in the field can serve as a valuable mediator and translator. Their in-depth knowledge of lateral flow test development and manufacturing enables them to navigate technical jargon, overcome communication barriers, and facilitate a smooth exchange of ideas. Acting as a bridge, the consultant helps the customer articulate their requirements and expectations, while also assisting the contract developer and manufacturer in interpreting and implementing those ideas accurately.
By engaging a consultant who possesses a thorough understanding of lateral flow test design and manufacturing processes, both the customer and the contract developer can benefit from streamlined communication, reduced misunderstandings, and improved collaboration. The consultant's expertise in this specialized field allows them to effectively convey technical concepts, address feasibility concerns, and align the customer's objectives with the practicalities of test development.
2. Choice of Materials, Including Nanoparticles and Antibodies
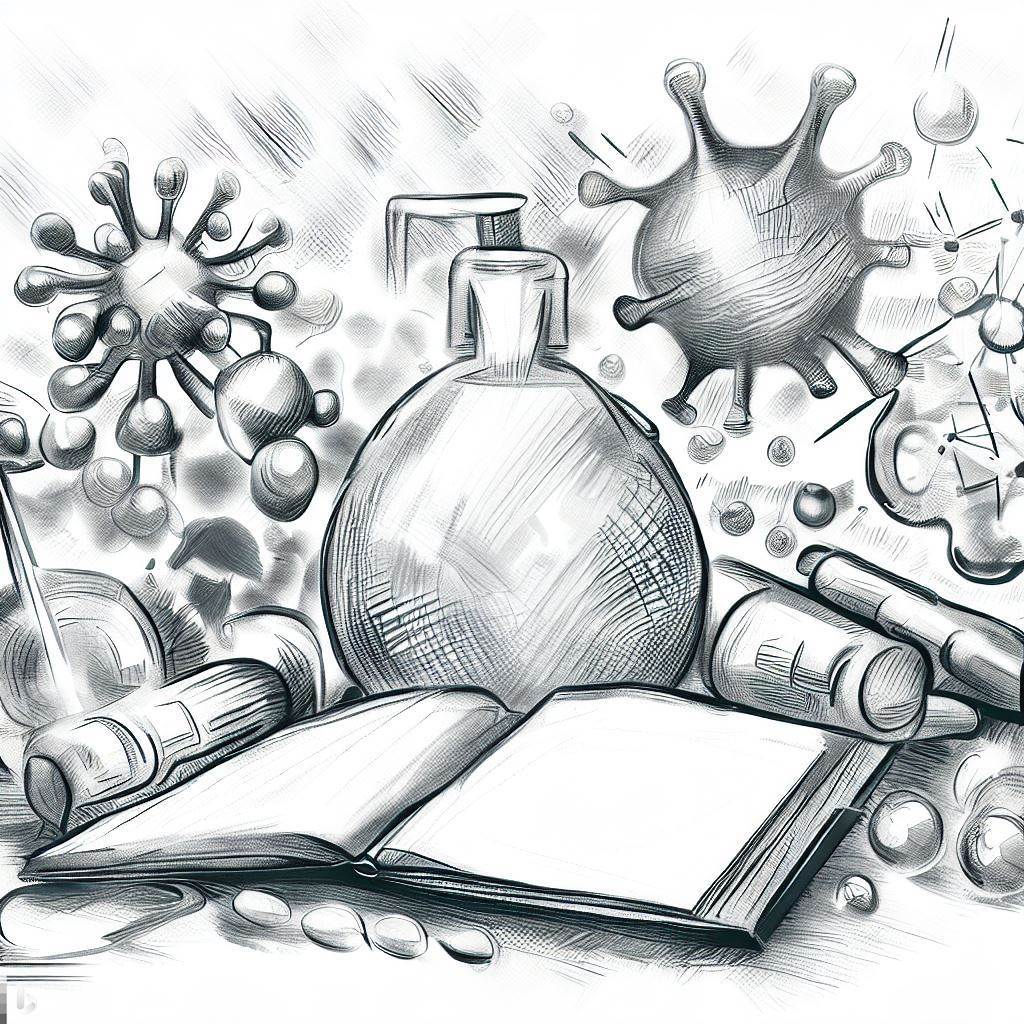
The selection of materials is a critical aspect of developing effective lateral flow tests. Two key components of these tests are the nanoparticles and antibodies utilized for detection. The choice of nanoparticles, such as gold or latex, can significantly impact the sensitivity, specificity, and overall performance of the test. To delve deeper in this special topic, please kindly refer to my respective blog post. Similarly, the selection of antibodies, whether monoclonal or polyclonal, must be carefully considered to ensure proper target recognition and binding affinity. However, finding the optimal combination of materials can be a complex endeavor, influenced by various factors.
During the development stage, extensive research and characterization of different materials are essential to identify those that best suit the specific requirements of the lateral flow test. Factors such as the target analyte, sample matrix, and desired sensitivity need to be taken into account when selecting nanoparticles and antibodies. Iterative optimization and validation processes are often necessary to fine-tune the material choices, combinations and concentrations for optimal performance.
Moreover, the (commercial) availability and sourcing of high-quality materials can pose challenges. Obtaining reliable and consistent quality of nanoparticles and antibodies, especially in large quantities, can be a daunting task. Collaboration with reputable suppliers and manufacturers is crucial to ensure the availability of materials that meet the necessary quality standards. Rigorous quality control and validation measures must be implemented to verify the performance and consistency of the selected materials.
3. Scale-Up Challenges
Scaling up the production of lateral flow tests from the laboratory to large-scale manufacturing presents a unique set of challenges. While a prototype may exhibit promising results in a controlled environment, the transition to mass production requires careful consideration of several factors to ensure consistent performance and quality.
One of the primary challenges in scale-up is maintaining the reproducibility of the test across large batches. Variability in manufacturing conditions, such as temperature, humidity, and equipment settings, can influence the performance of the lateral flow test. Optimization of manufacturing processes, through in-process-controls, standard operation procedures and robust quality control measures – including trained and well instructed operators - are essential to minimize batch-to-batch variations and ensure consistent test results.
Another significant challenge lies in sourcing and securing the necessary raw materials and components in large quantities. As demand increases, maintaining a reliable supply chain becomes crucial. Collaboration with trusted suppliers and manufacturers, along with strategic inventory management, is necessary to avoid disruptions in production and maintain product quality.
Additionally, automating and streamlining manufacturing processes is essential for efficient and cost-effective production. Developing automated systems for process like dispensing, assembly or even quality control can enhance throughput and minimize human error, thereby increasing productivity during scale-up and routine production.
During scale-up, it is vital to validate the performance and reliability of the manufactured lateral flow tests. Comprehensive validation studies, including stability testing, cross-reactivity assessments, and (clinical-) evaluations, are essential to ensure that the tests consistently meet the desired performance criteria.
4. Regulatory Hurdles
Navigating the regulatory landscape can be an unrewarding task but nonetheless crucial aspect of developing and manufacturing lateral flow tests. Regulatory bodies around the world impose specific requirements to ensure the safety, efficacy, and quality of diagnostic devices. However, meeting these regulatory hurdles can be a complex and time-consuming process.
The regulatory pathway for lateral flow tests involves demonstrating conformity with applicable regulations and guidelines. This typically includes conducting rigorous analytical and (clinical-) performance evaluations, as well as comprehensive documentation of the development and manufacturing process. Obtaining regulatory approvals or certifications, such as the CE mark in Europe or FDA clearance in the United States, is often required before the tests can be commercialized and distributed. This is also a ofttimes underestimated cost-factor.
The process of obtaining regulatory approvals involves submitting detailed technical documentation, including i.a. risk assessment, performance data, stability studies, manufacturing records, and quality control procedures. Demonstrating the analytical sensitivity, specificity, and reliability of the test is of highest importance for regulatory compliance. Additionally, compliance with relevant quality management systems, such as ISO 9001 or even 13485, is often required to ensure consistent product quality.
Understanding and staying updated with the evolving regulatory requirements can be challenging as well. Engaging regulatory experts or consultants with expertise in the field and also the notified bodies themselves can provide invaluable guidance throughout the regulatory process. These experts can help interpret the regulations, assist with the compilation of the required documentation, and facilitate communication with regulatory authorities.
It is important to note that regulatory hurdles may vary depending on the intended use and target market of the lateral flow test. Regional variations in regulatory frameworks and requirements necessitate careful planning and engagement with regulatory authorities early in the development process to avoid delays and ensure compliance.
Section 5: Sourcing of Samples, Real Samples, Internal Standards, Calibrators, Quality Control Material
The accurate and reliable performance of lateral flow tests relies heavily on the quality and availability of appropriate samples, internal standards, calibrators, and quality control materials. These components play a critical role in ensuring the sensitivity, specificity, overall performance and long term consistency of the test.
Sourcing authentic and representative real samples is vital for validating the performance of the lateral flow test. These samples should closely resemble the target analyte found in clinical or environmental settings. Obtaining a diverse range of real samples that cover the full spectrum of analyte concentrations and matrices can help assess the robustness and accuracy of the test under real-world conditions.
Internal standards and calibrators are essential for ensuring consistent and accurate quantification in lateral flow tests. Internal standards, typically analytes with known concentrations, are incorporated into the test to monitor the performance of the assay, account for potential variations, and validate the test results. Calibrators, on the other hand, are used to establish a quantitative relationship between the test results and the target analyte's concentration, enabling reliable interpretation of test outcomes.
Quality control materials are indispensable for maintaining the reliability and consistency of lateral flow tests during manufacturing and throughout their shelf life. These materials, which mimic the test samples, are used to assess the precision, accuracy, and overall performance of the test. Including quality control steps in the manufacturing process allows for ongoing monitoring and verification of the test's performance to ensure that each batch meets the necessary quality standards.
When sourcing samples, internal standards, calibrators, and quality control materials, it is crucial to ensure their stability and traceability. Proper storage conditions and shelf-life assessments should be conducted to guarantee the long-term viability and accuracy of these components. Collaboration with reputable suppliers and adherence to strict quality control protocols are paramount to maintain the reliability and consistency of the lateral flow tests.
In conclusion, the development and manufacturing of lateral flow tests come with their share of challenges. Addressing issues related to the transfer of ideas, material selection, scale-up, and regulatory compliance is essential for successful commercialization. By establishing effective communication channels, carefully selecting materials, optimizing manufacturing processes, and engaging with regulatory experts, developers and manufacturers can overcome these challenges and deliver reliable and accurate lateral flow tests for various applications. These tests play a vital role in enabling quick and accessible diagnostics, making a significant impact on healthcare, environmental monitoring, and other industries.
If you like to discuss those topics in more detail, don’t hesitate to contact me and book a meeting. Share your own experiences, ideas, or challenges related to lateral flow test development and manufacturing and send me a message.
Disclaimer: All Pictures and Sketches were produced by AI Bing Image Creator.
If you like to discuss those topics with me, don't hesitate to book a meeting!
References:
U.S. Food and Drug Administration. (2022). Emergency Use Authorizations. Retrieved from https://www.fda.gov/medical-devices/emergency-use-authorizations-medical-devices/covid-19-emergency-use-authorizations-medical-devices
European Commission. (2022). CE marking. Retrieved from https://ec.europa.eu/growth/single-market/ce-marking_en
Global Harmonization Task Force. (2012). Principles of In Vitro Diagnostic (IVD) Medical Devices Classification. Retrieved from https://www.imdrf.org/sites/default/files/docs/ghtf/final/sg1/technical-docs/ghtf-sg1-n77-2012-principles-medical-devices-classification-121102.pdf
DCN Dx. (n.d.). Assay Development Issues: From Lab to Market. Retrieved from https://dcndx.com/blog/assay-development-issues/ - 14-Jun-2023